Mixing nozzles are essential for the correct installation of chemical anchors. It’s important to remember that chemical anchor cartridges are two-component products that are of no use separately.
The first of the components is commonly called resin or mortar and the second is usually known as reagent or catalyst.
When both components are mixed properly, and in the quantities stipulated by the manufacturer, they react and are used to fix threaded rods or reinforcements in different base materials.
Nozzles are used to create the right mixture. These elements make sure that the mixing occurs properly while the cartridge is extruded. They are plastic elements with an internal helix that mixes products together as the product is extruded with the application gun.


The first extrusion of the already mixed product should be discarded until (always following the installation instructions) it acquires a uniform colour and texture. At first, they are usually darker and runnier than when they are mixed correctly.
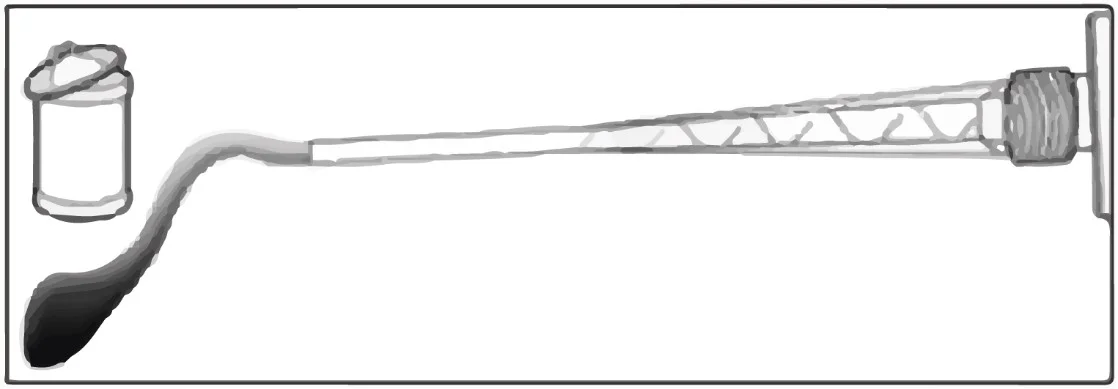
As well as fulfilling their main function, described above, the nozzles can serve a double purpose. When a cartridge has not yet been fully extruded, it helps to keep the components in their original state by simply leaving the used nozzle threaded onto the cartridge. The product will only harden at the tip of the nozzle, where the mixture of the two components has already taken place. When you next use it, you will just have to replace the nozzle with a new one and discard the first few centimetres of product again. We do not recommend unscrewing the nozzle and putting on the cartridge cap as this might cause some partial mixing to occur in the cartridge nozzle and the cap cannot be unscrewed at a later date
CAREFUL!
Often, users who have not finished using a cartridge, but whose mixture has hardened at the tip of the nozzle, tend to cut the nozzle off allowing the cartridge to be fully extruded. Although a small cut should not cause too many problems, it’s common to see users cutting the nozzle too much, preventing the two components from mixing correctly. As a result, fixings with inadequate mixes are common, resulting in unsafe and inadequate installations. Under no circumstances does INDEX recommend cutting the nozzle. Instead, they should be replaced when required for the extrusion of the product.
Finally, you should be aware that not all nozzles are valid for all types of cartridges. Depending on the proportion type of the components inside the cartridges, a certain type of nozzle should be used. At INDEX, we currently have 2 groups of nozzles, MORCANU and MORCAPU. They are easily distinguishable as the MORCANU has a more cylindrical shape while the MORCAPU has a rectangular prism shape. The first is used for all those products in the INDEX range that have a ratio between resin and reagent of 10:1 (300 and 410 ml cartridges). The second is used for more equal proportions, such as 3:1 and 1:1 (385, 585 and 600 ml cartridges). For further details, see the table below:
PRODUCTS | ![]() MORCANU | ![]() MORCAPU |
![]() MO-PU | ![]() | ![]() ![]() ![]() ![]() ![]() ![]() ![]() ![]() ![]() |
![]() MO-P+ | ![]() ![]() ![]() ![]() ![]() ![]() ![]() ![]() ![]() | ![]() ![]() ![]() ![]() ![]() ![]() ![]() ![]() ![]() |
![]() MO-PS+ / MO-PSP+ | ![]() ![]() ![]() ![]() ![]() ![]() ![]() ![]() ![]() | ![]() ![]() ![]() ![]() ![]() ![]() ![]() ![]() ![]() |
![]() MO-V | ![]() ![]() ![]() ![]() ![]() ![]() ![]() ![]() ![]() | ![]() ![]() ![]() ![]() ![]() ![]() ![]() ![]() ![]() |
![]() MO-VS | ![]() ![]() ![]() ![]() ![]() ![]() ![]() ![]() ![]() | ![]() ![]() ![]() ![]() ![]() ![]() ![]() ![]() ![]() |
![]() MO-H / MO-HW | ![]() ![]() ![]() ![]() ![]() ![]() ![]() ![]() ![]() | ![]() ![]() ![]() ![]() ![]() ![]() ![]() ![]() ![]() |
![]() MOPURE | ![]() ![]() ![]() ![]() ![]() ![]() ![]() ![]() ![]() | ![]() ![]() ![]() ![]() ![]() ![]() ![]() ![]() ![]() |
![]() MOPUR3 | ![]() ![]() ![]() ![]() ![]() ![]() ![]() ![]() ![]() | ![]() ![]() ![]() ![]() ![]() ![]() ![]() ![]() ![]() |
Latest revision: FAQ29 rev0