Chemical anchors are usually available in two different formats: plastic cartridges and glass capsules. In both formats we’re talking about two-component products. Therefore, regardless of the format, you’ll find both components inside: the resin and the reagent.
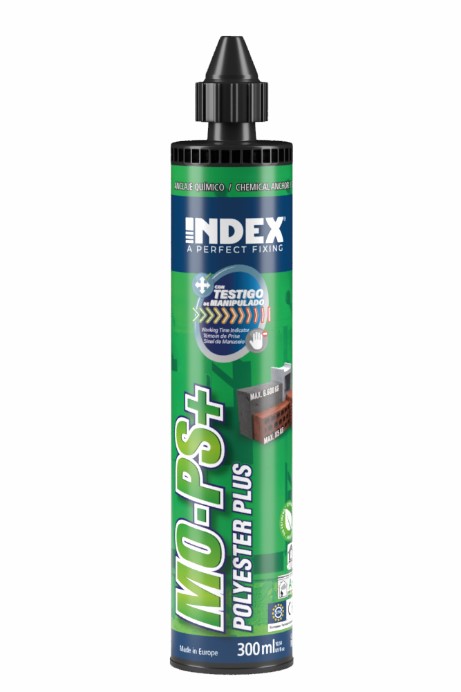
VS
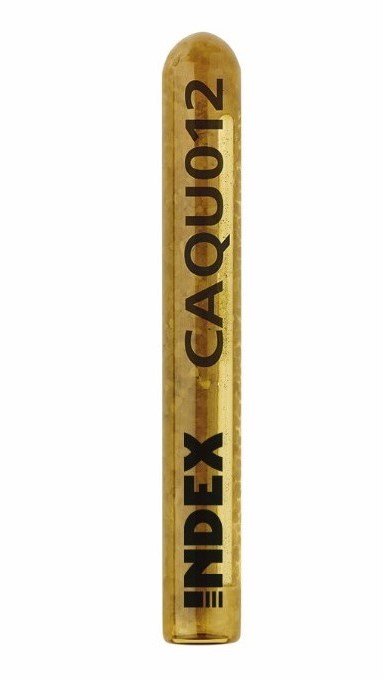
Although the two formats have many attributes in common and may appear to be similar in use and scope, there are very important differences. These are listed below:
1. Installation depth: While glass capsules have a fixed installation depth, fixings made with a cartridge allow installation at a range of depths. In other words, with anchors by injection using a cartridge we can adjust the installation depth according to the requirements of each case, installing at a shallower depth for low loads or at a greater depth for more demanding cases.
IMPORTANT: Chemical capsules cannot be stacked one on top of the other. Such a fixing would not be covered by the product approval and the performance of the product could not be guaranteed.
2. Residues: The chemical capsules contain both components within the format itself and their mixing is done inside the hole during the installation of the metal stud. In the case of cartridges, however, this mixing must be done through the mixing nozzle, discarding the initial part of the product until a homogeneous mixture is reached. This process involves the generation of waste, which, although not abundant, is greater than that of capsules. In addition, in the case of anchors installed by injection, when the metallic element is inserted it is likely that product will overflow from the anchor mouth, and this must be removed.
3. Accessories: To install a chemical anchor it is necessary to drill the hole and clean it with both a brush and an air pump. The hole is then filled with the chemical anchor and the metal element is inserted. To carry out these actions, the elements common to both formats are: drill, drill bit, air pump, brush and metal element. However, for the extrusion of the cartridge you’ll need to have an applicator gun for each cartridge format and a specific mixing nozzle. In the case of the chemical capsule, you’ll need to have a low speed screwdriver to break the capsule by impact with EQ type studs; these studs must have a hexagonal head to accommodate a socket that allows them to be turned during installation.
4. Hole cleaning process: As both formats are anchors which operate on the principle of adhesion, cleaning the inside of the hole in the base material is critical to achieve the required product performance. However, the capsule installation process, where the stud must be inserted into the hole by rotating at low speed in such a way that it breaks the capsule and mixes the components together, generates a dragging effect of the remaining dust on the inner side of the hole, thus improving the adhesion of the product. The capsules are therefore less sensitive to how well the hole in the base material is cleaned.
5. Cost: While each case is distinct and there may be individual differences, in general terms the installation of chemical capsules is more costly. To achieve the same fixings, you’ll usually need to use a larger number of capsules than the cartridge equivalent, and capsules are generally more expensive.
6. Packaging: These products are packaged in master boxes. In the case of cartridges, these usually contain 12 units. Capsules are packed in master boxes which can contain between 6 and 10 capsules depending on the size. In addition to the differences mentioned above, it should be noted that chemical capsules are much more fragile due to their format and are much more likely to break in case of a fall than are the plastic cartridges.
7. Health and safety risks: As the capsule is made of glass, it is more susceptible to breakage during handling, which could result in injury to the operator.
8. Logistics: The glass capsules are more fragile and therefore need to be handled more carefully throughout the logistics cycle. Moreover, stock management is more complicated for capsules because the correct capsule dimensions must be used for each job, whereas cartridges are valid for all sizes of job.
9. Applications: Chemical cartridges are more versatile products and have more potential applications than chemical capsules. These applications include fixing in masonry, connection of post-installed reinforcement and fixing in cracked and non-cracked concrete which, with some exceptions, are not common applications of chemical capsules.