Products of chemical origin, such as chemical anchors, polyurethane foams or silicones, are subject to conditions dictated by temperature. The temperature variation can change the way they behave in many ways. Below, you´ll find a brief explanation to illustrate the differences between the different types of temperature:
- Storage temperature: this is the temperature at which the product should be stored and maintained to guarantee, once it is used, compliance with the performance outlined in the manufacturer´s technical documentation.
Failure to comply with this condition can also reduce the product´s useful life, making it impossible to remove it from its container, whether it be a cartridge or a metal container.
In the latter case, it can also, if kept at high temperatures for a prolonged period of time, even cause containers to explode, given that they contain compressed gases.
This temperature is usually between +5°C or +10°C and 25°C.
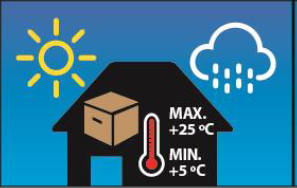
- Installation temperature: this is the minimum temperature of the base material to which an anchor can be installed; this information can be found in the technical documentation of the product. For low temperature conditions, it´s a good idea to use the “winter” versions. In any case, the chemical cartridge must be at a temperature above 5°C to make it easier to apply.
- Handling time and application temperature: for some products with the origin mentioned above, such as chemical anchors, temperature must be taken into account because it determines the handling and curing times. Others, such as silicones, have a temperature range at which they must be applied to guarantee proper curing.
First, with chemical anchors, we have to understand that they are bi-component products, that is, that inside the cartridge there are two different products (for example: polyester and catalyst). When the two come into contact with each other in the mixing nozzle, this initiates a chemical reaction that begins the handling time.
The handling time is the time we have from the application of the product, in this case the filling of the hole, until we insert the metallic element, be it a threaded rod or a corrugated bar. During the handling time, the product will be malleable and we can apply it easily; once the handling time has elapsed, the chemical reaction will have started and correct adherence between the stud/corrugated bar and the mortar will not be ensured.
The duration of this time will depend directly on the temperature of the base material. As an example, see the table of products MO-H and MO-HW in the table. - Curing time: this is the time required for the chemical reaction to be completed and the nominal strength of the fixation to be reached. Like all chemical reactions, the reaction speed depends on the temperature: longer curing times at low temperatures and shorter times at high temperatures.
Once this time has elapsed, the product will have reached its maximum resistance, now making it possible to install and fix the anchor plate. As an example, see the table of products MO-H and MO-HW.
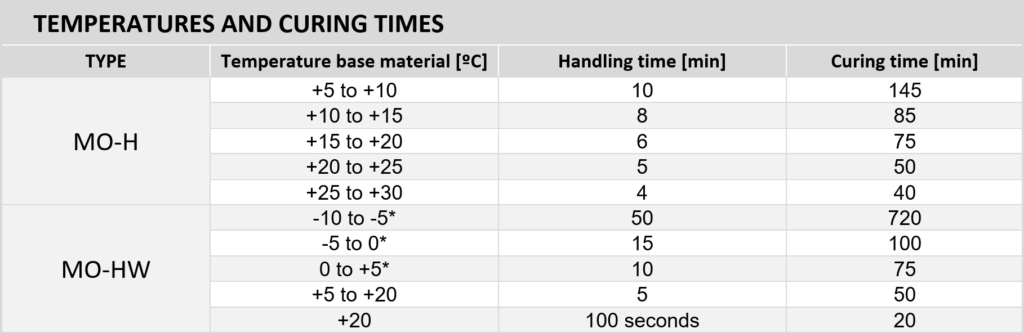
- Service temperature: the service temperature is the temperature range within which, once the product has cured, the performance outlined by the manufacturer in the technical documentation is guaranteed. In some products, the short-term service temperature (short variations throughout the day) or long-term service temperature (average values over several days) can affect the performance of the product installed; this effect is reflected in the applicable documentation. The usual range for chemical anchors is from -40°C to +50°C in the long term. For the rest of the products, consult the corresponding technical sheet.
Latest revision: FAQ17 rev0